Everything you need to know about choosing WPC Foam Sheet
WPC (wood plastic composite) Foam Board offered is a kind of furniture and building material made of polyvinyl chloride or PE (polyethylene) and PP (polypropylene) and rice husk powder, with features such as waterproof, flame retardant, acid & alkali resistance, light, heat preservation, noise insulation and shock absorption. It has the same processing method as wood. But compared with the processing performance, it is far more superior. Therefore, the WPC Foam Board can be the ideal substitute of wood, aluminum composite board, plywood, MDF, particle board. Furthermore, the surface is very smooth and of high hardness, which is not easy to scratch. For this feature, the WPC Foam Board can be the prime choice in making furniture.
It can be described in a few words as: attractive, durable, versatile, and as elegant as wood but without its flaws.
WPC Foam Board is made with Celuka or Co-extrusion structural foaming process system with high technological setups. Termite and pest proofing has made the board preferable for countless outdoors and interiors. It is also suitable for making doors and windows due to its high weather resistance. It rapidly replaces wood and plastic due to their limitations. WPC Foam Board projects its excellent favorable characteristics like environment friendliness, moisture resistance, water resistance, and aging resistance.
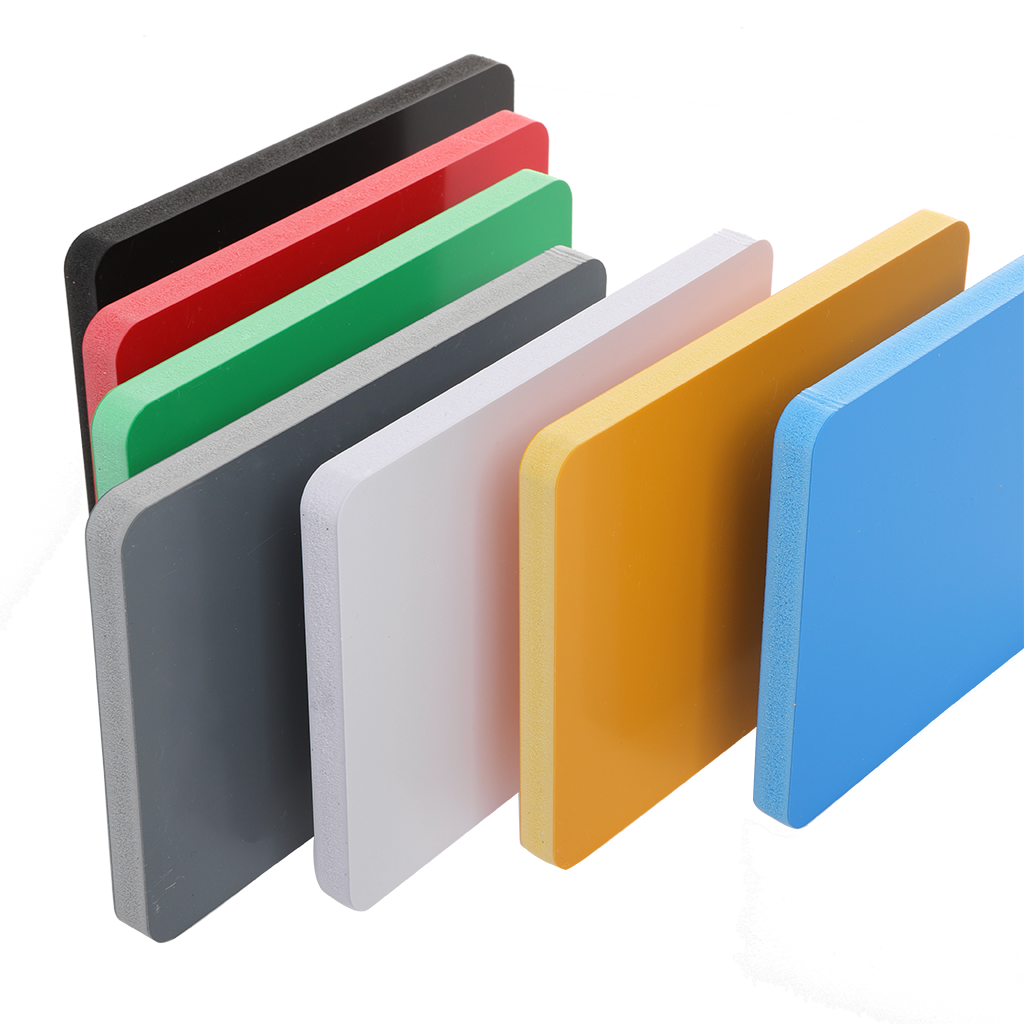
Explore & Discover recommended products
Characteristics
■ Environmental friendly, no any benzene and the formaldehyde discharge.
■ Energy saving, made from the waste lumber to get full use of the lumber.
■ Heat insulation and heat preservation
■ Waterproof, corrosion protection, shape keeping
■ Weather-resistance, can stand temperature between -30℃ to +70℃ , non-deformation, aging-resistant.
■ Fire retardant, automatically extinguish by itself and meet the standard of GB/B1.
■ Good mechanical performance, cut, hammered, drilled, sawed, turned, glued, bended, printed, oiled, thermoforming.
■ Perfect chemical resistance, good resistance to light, UV & weathering.
■ Good Impact strength. An entire 1220*2440*15mm sheet dropped from 12m high place, no break, nor deformed
Properties of WPC foam sheet
WPC foam sheets are available in two different grades: Co-extrusion and Celuka. The difference between these two foam sheets is due to two different manufacturing processes.
It is important to know the difference between the two types of WPC sheets because they each have their own applications and processing options.
The Co-extrusion process
Co-extrusion is the process of pressing two or more materials through the same mold to produce a single piece. In this process, two or more orifices are arranged in such a way that the fusion and interlocking of the extrusions takes place and a laminar structure is formed before cooling. In co-extrusion, a separate extruder is used to feed each material to the mold, but the orifices can be arranged such that each extruder supplies two or more layers of the same material.
Each co-extruder has a different laminate layer which gives a required characteristic property such as heat-sealability, rigidity and impermeability, all of which are impossible to achieve using a single material. When multiple plastics are combined, the result can yield properties distinct from those of a single material.
The Celuka process
Celuka is an inward foaming process used to extrude components with reduced density. The Celuka process suppresses cell formation at the surface creating a hard high-quality finish while allowing the hot melt to expand inward forming a cellular structure. The hard outer skin and fused inner core create a strong profile with multiple post finish options, fastener retention as good as wood, and excellent insulation properties.
WPC celuka/crust foam board is a kind of WPC foam board we recommended to our customers as they have superior quality. The extrusion line adopts celuka foam technology. These processes result in a “skinning” or outer layer of the foam board and harder or more scratch resistant. Compared with other WPC foam boards, this kind of WPC foam board not only has much more smooth surface, but also has better skin hardness, and the mechanical performance of the WPC celuka foam board is much better than other WPC foam boards.
Applications of WPC boards
Panelling: This material is quite long-lasting, and because it comes in various sizes, it may be used for both interior and outdoor panelling.
Furniture: Best material to carve out the furniture of your choice meeting the up to date trends.
WPC board for Interior: WPC boards are also utilised in the interior sections to make various furniture items like wardrobes, kitchen cabinets, interior walls, ceilings etc also the best option to craft and personalise your office space, living room etc. WPC board for kitchen is quite popular for its style and splendid features.
WPC board for Exterior: WPC boards can be used in exterior applications such as constructions, outside wall cladding, garden furniture, park benches and fencing, prefabrication houses, various exterior applications, and outdoor deck flooring. WPC foam board furniture generally lasts for years. Hence today’s most trustworthy product.
Advantages of using WPC boards
WPC boards are known for their high quality. These boards contain stabilizing agents, modifiers, foaming agents, and other ingredients that must be mixed in a precise ratio. WPC boards become a high-quality material as a result of the right blend of high-quality elements and that’s the reason why, WPC board dealers near me, is a most enquired question on the internet today.
WPC can be shaped and sized in a variety of ways. Hence, WPC exterior cladding is also quite famous. It has a very rich appearance and the best polishing. It is utilised for household furnishings, interior and exterior works mainly because of this.
WPC is a fire-retardant material. It protects your exclusively crafted products from fire and keeps them safe.
WPC boards are given a modern and high-end surface treatment, such as paint or thermal transfer, to make them look flourishing. The skilled surface treatment not only offers the WPC boards a different appearance but also gives them a ravishing tone.
It is a safe and environmentally friendly substance to use. It is water repellent, fire, and chemicals while remaining unspoiled and unaffected by climatic conditions.
It’s a promising and cost-effective plywood replacement.